Unveiling the Art of Precision: Creating High-Quality Plastic Bottle Blow Molds
1. Plastic Bottle Blow Molds
The manufacture of plastic bottles is a crucial aspect of various industries, including food and beverage, cosmetics, and pharmaceuticals. **Plastic bottle blow molds** serve as the foundation for creating these essential products. Understanding the intricacies involved in creating high-quality blow molds is vital for manufacturers aiming to enhance product quality and production efficiency.
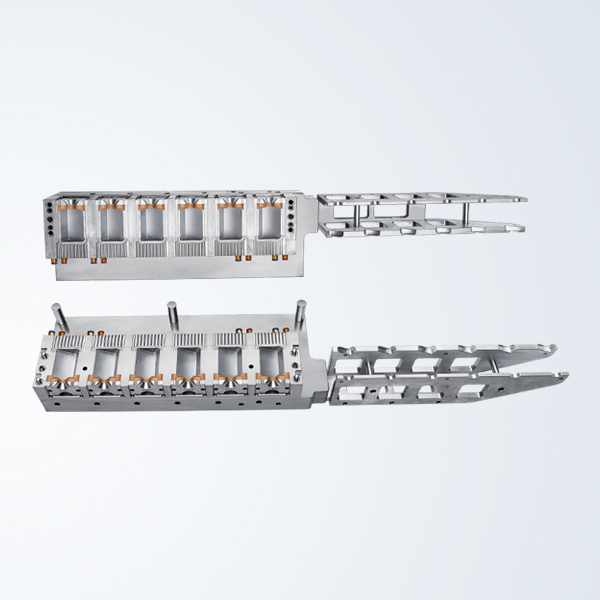
2. Understanding Blow Molding: A Key Manufacturing Process
Blow molding is a manufacturing process that involves forming plastic into hollow shapes, primarily for packaging purposes. The process entails heating plastic until it becomes pliable, then inflating it within a mold to achieve the desired shape. The three primary types of blow molding include:
2.1 Extrusion Blow Molding
In extrusion blow molding, molten plastic is extruded into a parison, which is then inflated into the mold. This method is widely used for producing large containers.
2.2 Injection Blow Molding
Injection blow molding combines injection molding and blow molding. Here, preforms are created using injection molding, which are subsequently inflated in a mold to form bottles.
2.3 Stretch Blow Molding
Stretch blow molding is particularly popular for producing PET bottles. It involves stretching the plastic before inflation, which enhances the strength and clarity of the final product.
Understanding these processes is essential for appreciating the role of high-quality molds in producing durable and reliable plastic bottles.
3. The Importance of High-Quality Molds in Production
The quality of plastic bottle blow molds directly impacts the efficiency and effectiveness of the blow molding process. High-quality molds contribute to several key aspects:
3.1 Improved Product Consistency
Consistent mold quality ensures that each bottle produced meets the required specifications, minimizing variations and defects.
3.2 Enhanced Production Efficiency
Well-designed molds facilitate faster production cycles, reducing downtime and increasing throughput.
3.3 Cost-Effectiveness
Investing in quality molds ultimately leads to lower production costs by decreasing waste and the need for rework on defective products.
4. Materials Used for Plastic Bottle Blow Molds
The choice of materials for manufacturing blow molds is crucial for achieving durability and precision. Common materials include:
4.1 Steel
Steel molds are favored for their strength and longevity. They can withstand the high pressures and temperatures involved in the blow molding process.
4.2 Aluminum
Aluminum molds are lighter and can be manufactured more quickly than steel molds. They are an excellent choice for low-volume production runs.
4.3 Composite Materials
Recent advancements have led to the use of composite materials, which combine the best attributes of steel and aluminum, offering a balance between cost and performance.
5. The Design Process: From Concept to Creation
Creating high-quality plastic bottle blow molds involves a meticulous design process. This process typically encompasses the following stages:
5.1 Initial Concept Development
Designers start by understanding the specific requirements for the bottles, including size, shape, and application.
5.2 CAD Modeling
Using Computer-Aided Design (CAD) software, designers create detailed models of the molds, which allow for precise adjustments and simulations.
5.3 Prototyping
Before finalizing the mold, prototyping is essential. Rapid prototyping techniques can help in creating a test mold to evaluate the design.
5.4 Final Design Approval
After thorough testing and adjustments, the final design is approved, paving the way for manufacturing.
6. Manufacturing Techniques for Precision Molding
Once the design is finalized, several manufacturing techniques come into play:
6.1 CNC Machining
Computer Numerical Control (CNC) machining enables precise cutting and shaping of mold components, ensuring accuracy in every detail.
6.2 EDM (Electrical Discharge Machining)
EDM is particularly useful for creating complex shapes. It uses electrical sparks to erode material, providing high precision.
6.3 Surface Treatment
Surface treatments, such as polishing and coating, enhance mold performance by improving durability and reducing friction during the blow molding process.
7. Quality Control in Blow Mold Production
Quality control is paramount in mold production. Several checks and tests are conducted to ensure that molds meet the required standards:
7.1 Dimensional Inspection
Molds are measured to ensure that all dimensions comply with the specified tolerances.
7.2 Material Testing
Testing the materials used in mold construction ensures they can withstand the rigors of the blow molding process.
7.3 Functional Testing
Functional tests evaluate how well the molds perform during actual production runs, identifying any issues that may arise.
8. Future Trends in Blow Molding Technology
As technology evolves, so does the blow molding industry. Key trends shaping the future include:
8.1 Automation and Robotics
The integration of automation and robotics is streamlining production processes, enhancing efficiency, and reducing labor costs.
8.2 Sustainable Practices
With increasing environmental concerns, manufacturers are exploring sustainable materials and production techniques to reduce their carbon footprint.
8.3 Advanced Monitoring Systems
Implementing real-time monitoring systems allows manufacturers to track production processes more accurately, leading to improved quality control.
评论
发表评论