Unlocking Precision and Efficiency: The Benefits of Dual Spindle CNC Lathes
In the realm of manufacturing and machining, the dual spindle CNC lathe stands out as a powerful tool that significantly improves productivity and precision. A dual spindle CNC lathe is equipped with two spindles that can operate simultaneously, enabling it to perform multiple tasks at once. This innovative feature not only reduces machining time but also enhances the overall efficiency of the production process.
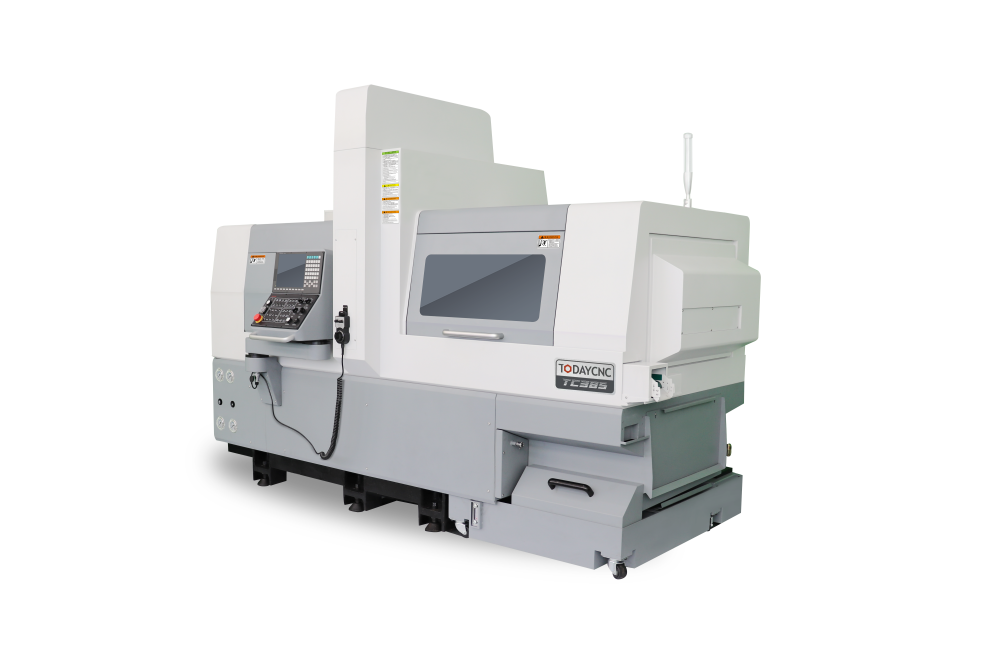
One of the primary advantages of dual spindle CNC lathes is their ability to streamline operations. In traditional machining setups, switching between different operations often incurs delays due to tool changes or repositioning of the workpiece. However, with a dual spindle system, manufacturers can achieve near-continuous operation by utilizing one spindle for the primary machining process while the second spindle can either perform secondary operations or even load and unload parts. This capability significantly minimizes idle time and maximizes throughput.
Precision is another critical aspect where dual spindle CNC lathes excel. These machines are designed for high accuracy, allowing for the production of intricate components with tight tolerances. The dual spindle configuration allows for more complex machining operations without compromising quality. As a result, manufacturers can produce high-quality parts that meet or exceed industry standards, catering to various applications in sectors such as aerospace, automotive, and medical device manufacturing.
Moreover, the versatility of dual spindle CNC lathes is noteworthy. They can handle various materials, from metals to plastics, and are suitable for machining operations, including turning, drilling, and milling. This flexibility makes them an ideal choice for job shops and manufacturers who need to adapt quickly to changing production demands and complex project requirements.
Implementing dual spindle CNC lathes in a manufacturing environment can lead to significant cost savings in the long run. By reducing cycle times and increasing operational efficiency, businesses can lower labor costs, minimize waste, and optimize resource utilization. Furthermore, the ability to produce high-quality parts consistently enhances customer satisfaction, ultimately contributing to a company's reputation and competitiveness in the market.
In conclusion, dual spindle CNC lathes represent a significant advancement in machining technology, providing manufacturers with the tools necessary to enhance productivity, precision, and versatility. As industries continue to evolve and demand higher standards of efficiency and quality, embracing dual spindle systems can be a game-changer for manufacturers looking to stay ahead in a competitive landscape. Whether for high-volume production or complex custom parts, the dual spindle CNC lathe is an invaluable asset in modern manufacturing.
评论
发表评论